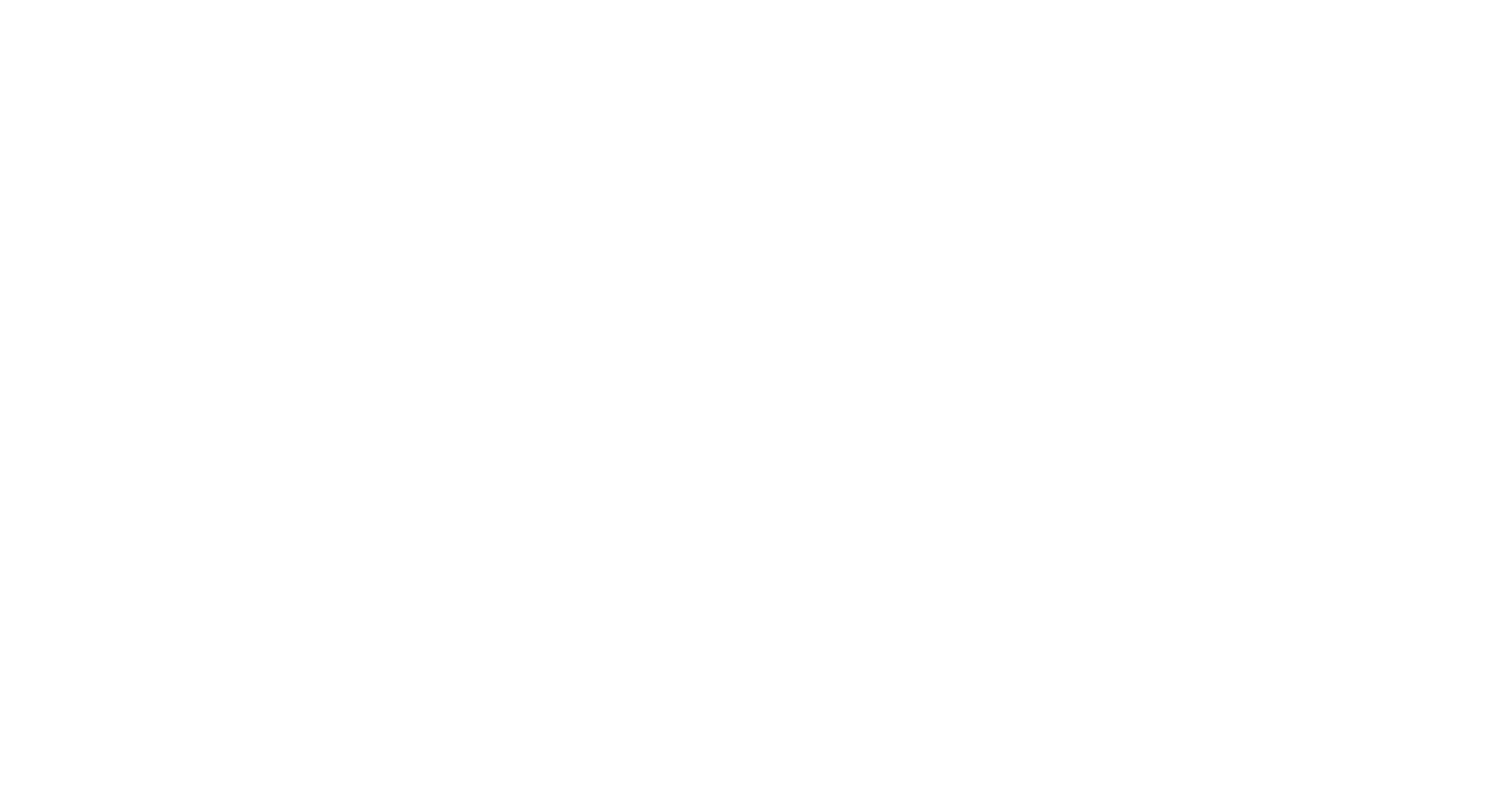
d2w
Members-
Posts
192 -
Joined
-
Last visited
Contact Information
Recent Profile Visitors
The recent visitors block is disabled and is not being shown to other users. |
-
Check the basics first; How tight is the bolt which snugs the lever to the housing at the pivot point? Is something restricting that movement? Check the fluid level in the master cylinder.
-
Consider the spherical bearings on the shock ends; they're a metal-to-metal interface which could squeak if dry. Carefully punch out the bushings/guides and then you can force grease into the ball track.
-
So this is the Google docs file.
-
But like my dad said: "At its worst, free advice is worth what you paid. Nothing!".
-
Hmmm garydwall ... I took a better look at the picture you took of the bearing; is that "metal seal" only partially covering the inner/ball cage? If so perhaps your idea to remove the inboard (i.e. tranny output shaft side) rubber seal is a very good one as the original bearing design kinda implies that the bearing is to be lubricated by the tranny oil. Like I said, I'm not a professional mech, but I do enjoy learning.
-
Hey garydhall. I found this video; thought it might help with your recent efforts. With full credit to Jim Snell: Regarding your question about using a bearing with a "rubber" sides vs metal sides, I wouldn't think it would be an issue. I don't believe the bearing environment would become so hot that the rubber might be compromised, or that heat transfer is an issue. I would not remove the covers however; perhaps the tranny oil would tend to "wash away" the bearing grease if the covers were not present. I don't know if the bearings expect to be lubricated by the tranny oil. So, in my opinion, I'd use the bearing as-is. Note, I'm only a do-it-yourself garage mechanic, so, as they say, "your mileage my vary".
-
FYI ... I've not done the work you're doing ... but I >believe< that the bearing is "special" in that there's an oil passage hole in the outer-race, and it must be aligned with an oil feed "pipe" in the casing. It is possible that I've mixed-up that requirement for alignment with the clutch-side bearing; I know one of them is "special". Just be mindful of the possible requirement. Dale
-
And I have one as well: 2008 GG 280 TXT PRO. With Paioli. My 2008 (the 280 is my son's) GG 300 TXT PRO has Marzocchis. Must have been a supply issue. I believe Beta uses Paioli forks as standard equipment.
-
Nice to hear. Search this forum on how to start a Gasser; there's a definite procedure required. But once you commit to the practice, you'll be rewarded.
-
Or try this: 1) Clean the remaining case thread well. 2) Clean the hollow/"banjo-bolt" well. 3) Lightly heat the bolt and apply a thin coating of paraffin (aka candle) wax to the threads. 4) Mix well some J-B Weld epoxy. 5) Apply the epoxy to the threads and insert into the case. 6) Once the epoxy cures you should be able to extract the bolt, and reassemble. The tricky bit is to only retighten the bolt to seal the hydraulic oil but not destroy the epoxy threads. I suggest using a fresh/new set of copper crush washers to maximize your chance of getting a good seal. Dale
-
What Glayne is saying is that you need multiple bikes; it's the only solution. Hmmm ... there is a second solution: you ride your trials with your enduro buddies, but you lead. And show no mercy! 😏
-
I own two 2008's; one for me and one for my son. They bring a smile to our faces every weekend. But I'm prepared to wrench on them. I've modified the shocks to be easily recharged. And I'm prepared to cobble things together to make them work. No issues. No plans to replace.
-
Like this? https://www.splatshop.co.uk/engine-kill-switch.html or https://www.splatshop.co.uk/kill-light-switch-on-off-toggle-switch.html or https://www.splatshop.co.uk/leonelli-kill-switch.html
-
Tacton, I found some photos of my tranny. My photos show the shift drum in the same orientation. That being said ... one thing that *may* have caught my eye when looking at your old photos above and comparing them to mine ... on the shaft with the two shaft with the two shift forks... is the lower one flipped? The beveled edge looks to be oriented different than mine? Bit perhaps it's just a photo angle thing since maybe the guide pin only allows the fork to be installed one way? Anyways, here are some photos for reference. Again, these photos are from a 2008 GG PRO TXT300.