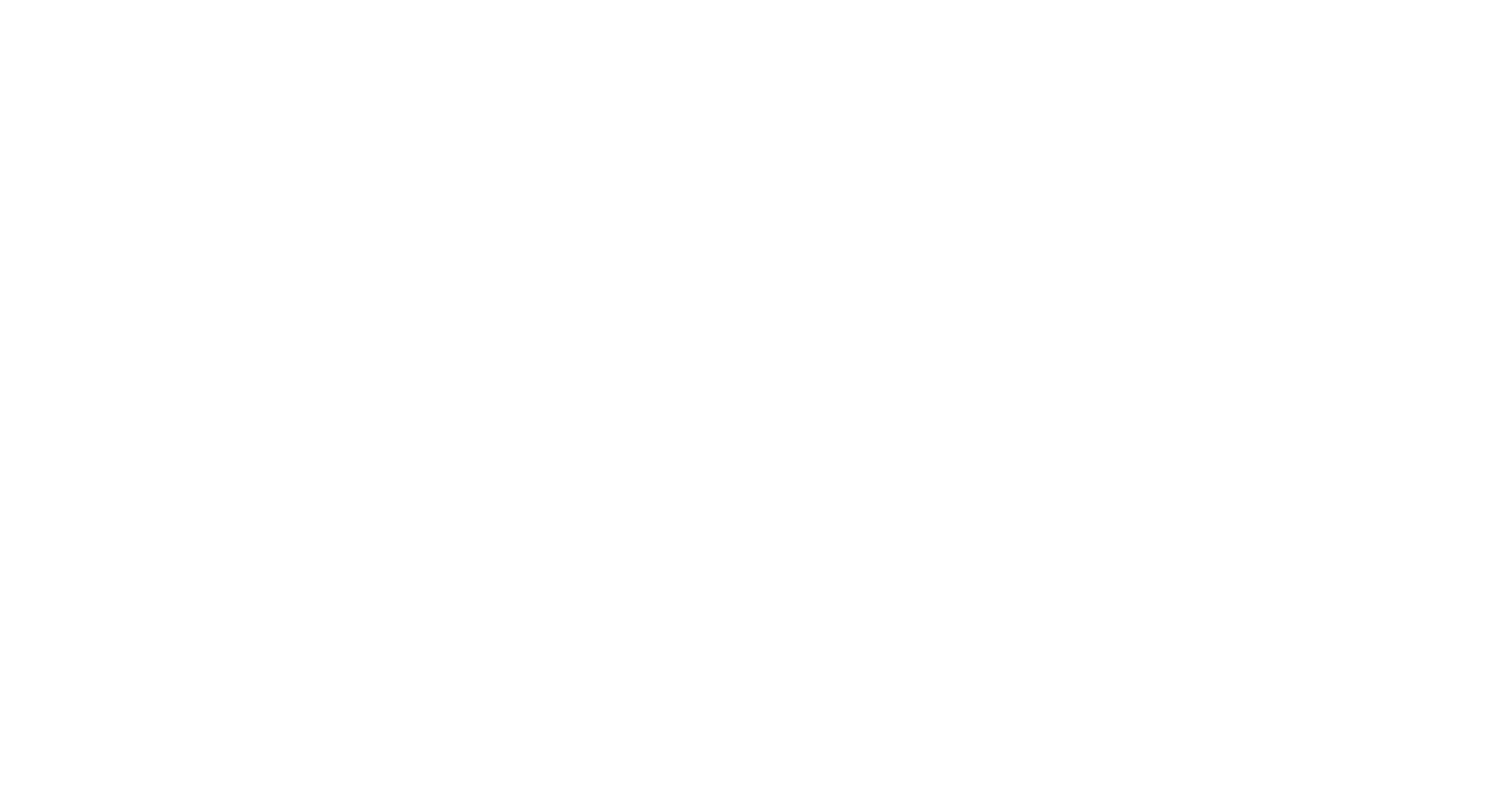
trial bike
Members-
Posts
59 -
Joined
-
Last visited
Contact Information
Recent Profile Visitors
The recent visitors block is disabled and is not being shown to other users. |
-
You can feel gyroscopic forces at work quite easily and demonstrated quite well with a large bicycle wheel. For anyone that is interested or not done it before ( probably as a kiddie taking his/her bike apart?). Hold the ends of the wheel spindle in each hand and roll the wheel along the ground ( or ask someone else to spin it for you) as fast as possible. Then try turning it left and right or tipping to the left or right. You will feel gyroscopic forces. This happens to any spinning thing, crankshaft, camshaft, flywheel, front wheel etc. It is why counter steering works to good effect on a road bike at speed and is one reason a two stroke feels more nimble than a four stroke, lighter and fewer spinning parts.
-
In the UK, any road helmet must be built to British Standard BS6658:1985 and carry a BSI Kitemark. They can be upto equivalent EU standards offering the same protection levels as BS6658 and should carry the equivalent mark. I don't think many trials helmets are road legal. They tend to be designed to be light, flow lots of air and to protect against low speed impacts. Having said that, I don't know how the SSDT guys get on?
-
Interesting reading.
-
Someone has just commented that they see people with too much air pressure in their tyres. Is it possible to have too little pressure? I worry about damaged rims if I run too low. I weigh nearer to 70kg than 80kg, ride a 4RT and run about 4psi on the rear. Sometimes I struggle with grip and think I should try lower pressure. But then I run onto rocks and think that would be a bad idea. What is your opinion?
-
Interesting point about the stiffness with age, I hadn't considered that. (Except in my knees)
-
Hi folks, I know this is an extremely debatable subject. (Do you ride mud, rocks, for pleasure or to win, etc) I'm just trying to get a feel for how long people keep a tyre going and whether sharp edges are the be all and end all. I have a rear on a 4RT with about 40 to 50 hours of grass slopes and rock sections, practising front wheel lifts and upto 2 foot steps, mainly. The front edges are quite well rounded now. But I still find grip doing tight turns on steep wet grass. I struggle finding grip in mud, but that is probably lack of practise and technique. How often do you change your rears? Do you ever "turn them round" to use the rear edges of the blocks?
-
You don't need to ratchet the forks fully compressed, which could put the seals under prolonged pressure that they are not designed to take. Just compress them enough to stop your straps rattling loose when the van/bike bounce around over bumps. It doesn't need a lot.
-
Hi, Some good advice here. My Mont has so much grunt and instant take off I don't think I have ever used full throttle on the stuff I ride, barely even half throttle. It'll climb just about any hill I have the guts for without having to rev much at all. It also takes off for logs and steps without too much of a handful. So it always amazes me when I see/hear guys reving the nuts off. (Maybe that's the difference between 2T and 4T) My take on your throttle control issue could be that you are struggling with the enduro to trials scenario. I guess maybe you use the throttle kinda on or off? Try covering the front brake lever with one finger. If I don't rest a finger on the brake lever, I find, especially when concentrating on new moves, that it is hard to meter in the throttle gently, and therefore it is easy to give it a gob full when you don't intend to. Keeping a finger on the front brake gives me a reference point and it becomes very easy to make tiny adjustments or suddenly wake it up a bit without over doing it. Works for me.
-
Hi, I will try and upload some pics when I next undress her for a service. Give me a little while… It started when I removed the Bank Angle sensor, an unnecessary item if a magnetic kill switch is used. I wanted to remove the metal bracket and unused connector so started to unwrap the loom. Someone suggested moving the fan relay up to the headstock at the same time, because that is where its wires originate. (They don’t.) I was aware of a few unwanted connectors around the headstock, so I thought "Why don't I just go for it". The first thing I noticed is just how complicated Montesa made the loom. There are wires running in one direction just to turn round and run the other way again. I think there were about 8 earth wires up at the headstock, connected with a large plastic block, with no apparent reason for being there. Instead of separate earth wires from each requirement all being joined at the headstock. I now have one earth wire with a tee taken off near each requirement. (I noticed in the wiring diagram in the owner’s manual that one of the earth wires from the frame travels directly to the ECU. I guess the ECU needs a “clean” earth for reference, so have left that wire unmodified.) Getting rid of the excess connectors at the headstock leaves room for the fan relay, which would eliminate the extra cable sheath that runs parallel to the main loom under the tank. But...nearing completion...I wondered why I was adding the weight of the relay to the very top and very front of the frame, when its wires originate from behind the engine, (lower and more central). Removing the fan relay mounting tang and Bank Angle sensor and mount leaves a lot more room for the main wiring connectors behind the cylinder. They tuck in much better under the throttle body in the large plastic sock. This leaves plenty of room for the fan relay to be sited between the main connector sock and the capacitor. Thus the relay moves inboard with much shorter wires. (There were two separate power wires running through the loom to the headstock and then back in the separate sleeve to the relay, but on unwrapping the loom the two wires were tee’d together nearer to the supply point.) I now have one much shorter wire running direct to the relay and tee’d just before the relay. The blue/black also now runs direct to the relay instead of up and back. As standard, the fan motor wires and sheath run down to the coil, just to turn round and run up to the headstock, which gives a separately wrapped cable nestling between the vent pipes, HT lead and loom alongside the radiator. It is now history. I have routed it straight up from the motor, strapped to the engine vent pipe, and shortened it. The connector sits by the vent pipe canister. The fuel pump connector is the only other one under the tank now. (You may want to leave the Mapping Switch connector there. It is not applicable to my bike. I have left a tail of it at the ECU for future use if need be). With a few other bits shortened or removed, I have left over on the floor… 4 wire connector blocks and approx 110g of wire etc. consisting of approx… 1.95metres of red power supply. 2.45m of green earth. 0.7m of yellow/green 0.5m white/green 0.65 of blue/black plus approx 0.45m of the plastic sheath. Removing the support tangs for the BA sensor and fan relay etc, shaves approx 80g off the standard rectifier bracket. Plus, of course, the instigator of the whole project the BA sensor at about 110g. Add in the shortening of the fuel vent tube whilst redirecting it to the headstock (as per old days) and removing the steering lock, you get the 350g weight reduction. And, yes. It runs perfectly. It’s a bit long winded, but you did ask!
-
JohnnyC, Reading your post again after having done the Duggan suggestion, I think that is exactly what you meant, eh? I can't believe the difference it makes. Its given me much more confidence that the brake is going to be there when I need it. I don't have to keep looking down anymore to see if it is with in reach, and I don't have to keep shifting my foot forward. Like they say, the simple fixes are often the best.
-
Duggan. Spot on. I have just tried that myself. I didn't strap it all the way back, because it looked a little tucked in. I strapped it about 1/3 to 1/2 way back. It is nigh on perfect. A brilliant idea, should have thought of it myself. My foot is now a little further back on the peg, how I like it, and the pedal is right under the front of my boot. Simple and free! Thanks chap.
-
Hi 2s4s, I'm a little like you, I ride on my instep but nearer the front of it than the middle, I do roll back onto the rear of the footpeg to weight it. But my boot does not reach the lever. I understand we all lift the foot, gear etc, but gear changes are not usually at crucial moments like using the rear brake when weighting the rear end. I nearly endo'd yesterday because my boot missed the lever by a few millimetres. I know a bike will never be perfect, but my pedal could be lot better than it is. As for the dual control thingy...www.clake.com.au/ Thanks for the ideas.
-
johnnyc... Sorry pal, I can't picture what you mean. any chance of a picture? I have thought about cutting the lever shorter and having the end welded back on. Good idea or not?
-
That Clake setup is very interesting, relating to the MTB, rear brake lever on the handlebar has much more delicate control. I do like the sound of a finger operated rear brake. But... What about the balance of clutch and brake? I can understand it working nicely to stop endos, but what about control in...for example...slow full lock turns up and down a steep camber. It is also very pricey!
-
I bought a pair of wulfsport boots because they were relatively cheap, in the dealers where I bought my bike and fitted comfortably. They were very stiff when new but broke in quite quickly. I have had them over a year now and they are great. They have one or two scars in leather so have protected my feet ok They have become much more flexible than when new and are really comfortable. The sole is almost as good as new. It is a great value boot.