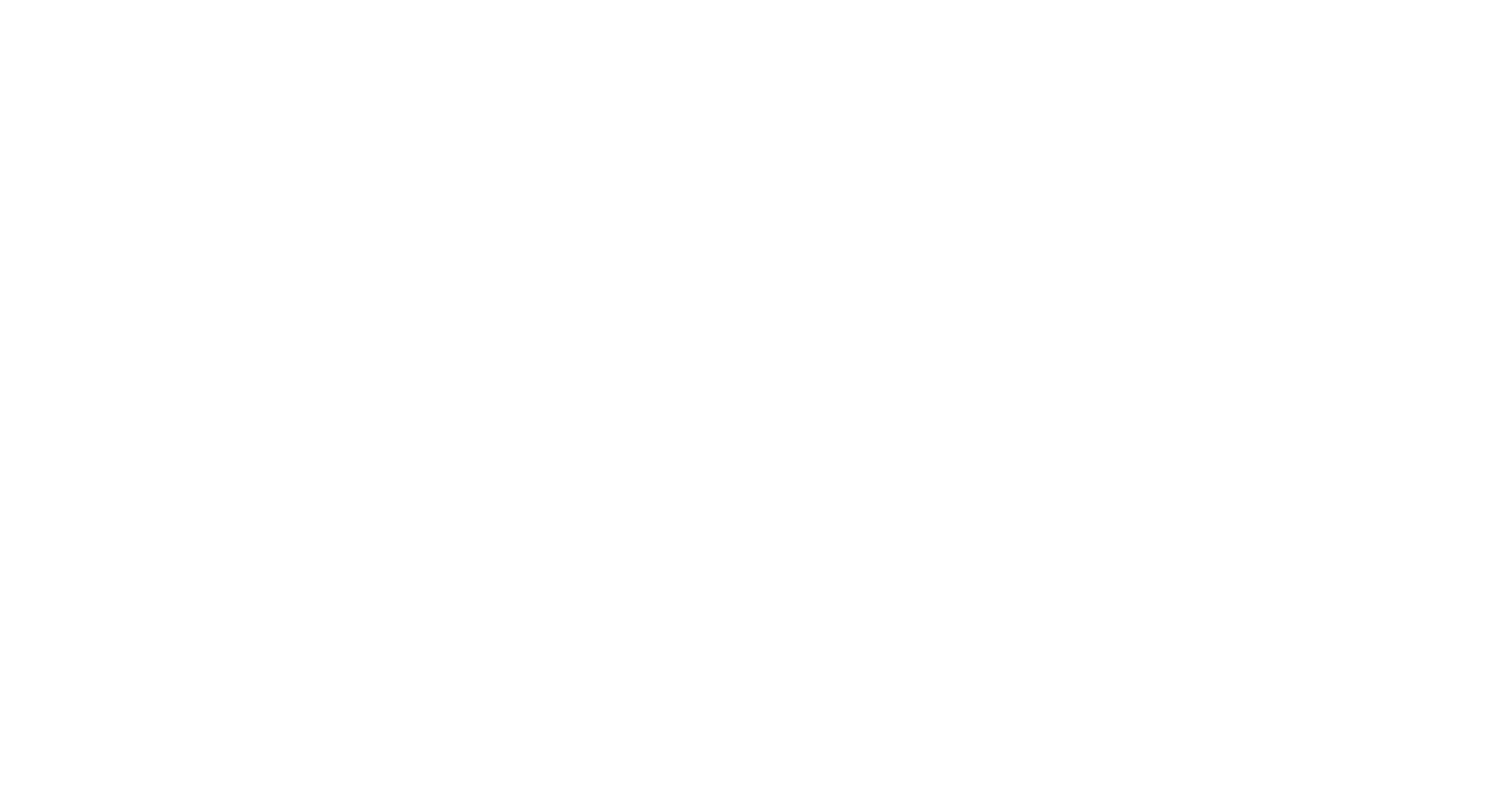
oz thumper
Members-
Posts
175 -
Joined
-
Last visited
Contact Methods
-
Website URL
http://
-
ICQ
0
Contact Information
-
HI Justin, I have not had this problem running 4RT's since 2005 so I can't speak from experience. However high current draw is usually what burns out electrical appliances. This occurs from excessive load on the unit,or LOW voltage. Low feed voltage increases the current draw (amps) . High voltage does not. Really high voltage can arc through the insulation or cause damage to electronics but not burn out wiring or motor windings. So don't agree that 14V will cause the fan motor to melt. Good luck
-
How can this work when both valves are opened by one rocker arm? Surely all you will measure is the tightest clearance? The other valve could be an excess clearance and you would not measure with a dial gauge?
-
In the UK a fastener threaded all the way was referred to as a "Set Scew" or 'Machine Screw" , Bolts always had a shank and a threaded section I believe to reduce the stress concentration around the head when subject to high torque and high tension loads.
-
I am around 62kg and have always found the Showa spring to be to strong and the damping to slow for me even when wound to full soft. Could not find a softer spring ready made (possible to have one made) I went with a TRP rear shock with a 62kg spring back in 2006 and found the TRP perfect for me and has not required any service despite regular competition use. I have just purchased a new aluminium body TRP for my 300RR, same excellent performance and approx 550gm lighter than the Showa and a reasonable price.
-
Hi Fred, on mine checked valve clearance when they became reluctant to start when hot (third or fourth kick not first kick). My 06 Repsol was after 54 trials (200 riding hours) and inlet were OK but exhaust were at the tight end of spec and immediate improvement in hot start after adjustment. My 2014 RR 260 was becoming difficult to start when hot and also very jerky motor response at low revs after 71 trials (logged as 314hrs.) On the '14 all valve clearances were at the tight end of the spec (i.e .03 under nominal value) but still just in the range given in the manual. Adjusted to the slack end of the range and an immediate significant improvement. I have to say the change in the 260 was not only in hot starting but the motor was so much smoother at the bottom end, it was like riding a different bike. My experience has been that the clearances are better set at the wide end of the quoted range and that they have remained stable for a long period after initial adjustment. It is a bit of a painful job getting to the tappets removing the injector etc. especially if some of the wiring connectors are reluctant to separate, they are hard to get hold of the connector body and I don't like to pull on the wiring loom -- no excuse but that is why I have not done them as regularly as maybe should. Good luck
-
Yes it is that simple. It is good to use a tachometer to set at 1800 but if not available just adjust the idle screw a bit at a time whilst listening to the motor. If you go to slow and it doesn't want to start readily, just adjust a little back the other way, it is not that fancy. I think that it also depends a little on the programme that you are running, My older 250RR I ran a soft bottom end programme (Zogg3 from memory) and the bike performed reliably with idle set down at 1200 rpm
-
That advice is correct however no one has asked if the fan is running while you are riding, if the fan does not run at least part of the time you have a fault and the motor will be hotter than normal leading to serious overheating.
-
My manual does have a table of standard torque values to be used when not otherwise specified. 6mm is 10 N-m and 8mm is 22N-m
-
Hi Chris, Exactly the same as my collection of bushes. I can add that after the first couple of failures I started orienting the bushes with the split to the front of fork leg, so that I could tell the position that the Teflon was peeling from. In my case it is the lower, rear section of the bushes. This eliminates any suggestion of the forks being out of line due to not centering the front axle. (In my case as noted in earlier post I have assembled front axle and fork bridge with the fork legs in full compressed position ) I too am convinced that it is a problem with the coating process because the damage does not extend vertically through the bush as would be caused by any fork tube damage. My dealer has sought advice from the factory but received no response, of the failures that I know of with the Showa forks all occurred after a short period from new and have continued following rebuilds, I have not had this on any of my previous Showa units. Are the race tech bushes manufactured by them do you know? I don't think the damage is mechanical from topping out, there are no marks on the edge of the bushing to indicate contact.
-
Whilst unlikely don't forget that tight valve clearance will also definitely affect ease of starting. It is generally preferable to set the valve clearance at the upper end of the book limit.
-
I have used the same system since '05 and never had a problem and yes mine gets plenty bent. I just use a good G cramp, prior to removing the plate I slip the G cramp over the bash plate at the rear and tighten up onto the cross frame (you can't get exactly central but doesn't matter) then slacken the front mount bolts about 5mm and then the undo the rear bolts and remove. Slacken the clamp off and remove front bolts. To replace, reverse process. With the clamp removed, start the front bolts and screw in about 3-5mm, then lift the rear of the bash plate, slip the G Cramp over as before and then tighten the cramp until the plate is close enough to start the rear mounting screws. When all well started tighten all screws and remove clamp. Believe me it takes longer to type than to fit the plate!! my G cramp is a 6 inch clamp. The reason I use the clamp when removing the bash plate is that it is easy to rip the last couple of threads out of the frame if you just undo the screws when the bash plate is badly sprung.
-
If you can't back bleed through the master cylinder check that the lever adjuster is not set tight, this will hold the master cylinder piston down in the bore and block off the return port. Just back the adjuster right off whilst back bleeding and it should flow straight through to the reservoir.
-
My 05 came with three restrictors in the exhaust system as you describe, the separate instruction leaflet accompanying the bike noted that they were for compliance reasons and should be removed for full power in competition set up. My dealer advised leaving the smaller diffuser at the end of the silencer to give max low speed torque. Over here the 06 Repsol came without any of the compliance parts such as lights and restrictors etc.
-
4Rt Cam Chain Tensioner..here's A Little Gem Worthy Of Remembering
oz thumper replied to richierich's topic in Montesa
Thanks for that really interesting information, particularly as there had been a previous post where most advice suggested the tensioner could not be a problem. Just goes to show there is always something new to learn on the forum. -
With the standard oil levels as per manual I find the forks pull up fairly suddenly on compression and are not reaching full stroke during a ride. I am thinking of reducing the oil level slightly to reduce the air spring pressure on full compression. I presume the left (spring) leg is the one that controls the final stroke, is that correct?? Have any light weight riders reduced the oil level and if so how much??